Combustion testing. The complicated question is, with nothing to adjust on a modern gas furnace aside from gas pressure and airflow, why even perform one? After all, of what benefit could it really be? Really? Why measures what you cannot adjust?
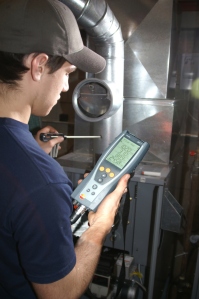
Furnace Basics you may have never considered.
Natural Draft
Natural draft or atmospheric appliances are relatively simple and as safe as modern appliances. In the case of an atmospheric burner, the combustion air is drawn in by buoyancy of the heated flue gasses and mixes with the fuel gas as it enters the combustion chamber. The fuel/air mixture burned in the combustion chamber quickly releases its heat (primarily by radiation) to the heat transfer surfaces surrounding it, and the hot flue gas escape through a draft hood into the flue. The role of the draft hood is to prevent excessive draft or a back draft in the venting system from affecting the combustion process and also to provide dilution air to assure flue gasses do not condense in the chimney. Because flue gasses have natural buoyancy, it is not necessary for the appliance to be connected directly to the flue to create flow through the heat exchanger. By design, as warm less dense air rises through the heat exchanger and moves toward the vent connector, fresh air will be required to replace it. Flue gas movement through the heat exchanger precisely controls the introduction of secondary air. So long as draft is provided at the vent connector, (which means the flue pipe must be cemented in at the chimney) the low-pressure zone created in the draft hood will direct all of the flue gasses and the proper amount of dilution air into the vent pipe and chimney. If a negative pressure is created in the appliance combustion/venting zone that is greater than the draft provided at the vent connector, spillage will occur. The flue gasses will always move to the area of lowest pressure. This will occur whether a draft hood or barometric damper is installed; hence the requirement of spill switches on both to improve safety.
Induced Draft/Forces Draft
The modern gas furnace is as susceptible to causing or having combustion problems as older atmospheric equipment, if not directly, often through guilt by association. Several factors including a more powerful circulation blower, tightly controlled excess air requirements, complicated venting requirements, combination venting issues and low mass complicated heat exchangers have all had an impact on performance and safety of these appliances. Remember, a new or correctly operating appliance can easily affect the operation of the combined vented hot water tank, or create depressurization within the home back drafting atmospheric appliances, fireplaces, wood stoves or pulling auto exhaust from an attached garage.
Many of the safeties incorporated into modern gas furnaces are required due to more complex heat exchanger and venting designs. Efficiency comes at a cost. Heat transfer has been increased by convection and residence time of the flue gasses in the heat exchanger. Because of these complex designs, the flue gasses no longer naturally flow through but are rather drawn through with a draft assist fan (draft induced). The function of in inducer on a mid efficiency furnace is to create a negative pressure on the heat exchanger, The pressure on the discharge side of the fan will also remain negative when connected to a properly designed venting system, as the inducer should never overcome the negative pressure created by the chimney draft. On condensing models, the induced draft fan performs two functions, creating a negative pressure on the heat exchanger and a positive pressure on the exhaust system to expel the byproducts of combustion. Pressure switches, roll out switches and fusible links all provide protection from a loss of draft or flow through the heat exchanger and ultimately reduce the risk of fire. Remember, a flame will travel toward its oxygen source. If combustion air is not entering the heat exchanger with the fuel, the flame will travel outside the combustion chamber in search of oxygen. Rollout switches and fusible links are designed to stop fuel flow by way of the gas valve should such an event occur. Draft induced appliances pose danger whether they are direct vented, or combined vented with an atmospheric appliance like a hot water tank. Even vented in PVC via sealed combustion, an improperly operating or vented appliance can pose a grave danger. Remember each appliance is part of a complete engineered system, which also functions as an independent system often referred to as the building envelope. In short, there is no gas or oil appliance; atmospheric, induced, ventless or other that does not require combustion testing to assure safe and reliable operation.
Ventilation Air Test
No combustion test should be completed until the venting system has been inspected, and safe removal of flue gasses can be assured. Building pressure testing can be a complicated science. Everything from stack effect to temperature, to prevailing wind can affect the pressures within a building. At the end of the day, you can have all the pressure measurements you want, but when the rubber meets the road, what’s really important is does the venting system really operate properly under even the worst conditions that could occur with the home.
The Ventilation Air Test, or Worst Case Depressurization Test should be performed every year on all atmospheric and induced draft appliances after an ambient CO test is performed. Additionally ambient CO should be monitored while performing the ventilation air test. Remember, CO can come from ANY fossil fuel burning appliance, so use caution while testing. The procedure for the ventilation air test is outlined in the International National Fuel Gas Code. (ANSI Standard Z223.1)
This procedure should be performed prior to any attempt at modification of the appliance or of the installation. This includes servicing, clean and checks, and/or mechanical changes. It should also be preformed after any new installation including that of a sealed combustion appliance.
If it is determined there is a condition that could result in unsafe operation, the appliance should be removed from service (shut off) and the owner advised of the unsafe condition. If there is not sufficient air for combustion and/or ventilation, the homeowner and/or technician will be at risk by operating the appliance under worst-case conditions.
This test is performed to insure that the building into which you are going to install, or have installed, a fossil fuel appliance has enough ventilation/infiltration air to replace the air used in the combustion and venting process. As homeowners are constantly making changes to the home, (caulking windows, adding weather stripping) this test should be performed on an annual basis.
(For additional information performing the ventilation air test, please consult the International Fuel and Gas Code or the Testo Combustion Guide)
Understanding that each appliance requires combustion testing is the first step in providing a reasonable standard of care to your customers. Performing the ventilation air test is critical to assure safe operation. Additionally, testing generates revenue and hopefully profit. Thousands of systems operate either constantly or intermittently with combustion/ventilation air deficiencies. Finding and correcting these problems not only increase customer safety, but also provides an additional revenue stream and service that should be part of every companies service procedures.
Sidebar
If you ever end up in a court of law, you will get a quick lesson in what standards are. Most tasks we perform in the HVAC industry can have a standard of care attached to it. A standard is nothing more than the usual and customary practices in the delivery of products or services within a particular business sector or generally accepted operating procedures, practices and requirements defined by national trade associations, and state and local government laws relevant to utility service. When it comes down to it, with all equipment inspection there is an implied warranty. The service technician must be aware that it has been upheld in court that unless the consumer is notified in writing that there is real, or potential problem; the person performing the inspection has determined that the appliance is operating safely and correctly. If you work in this industry in the capacity of a service technician, or installer, you are considered to be an expert. Furthermore, if it can be proved the technician (expert) was negligent in his or her job, they could be liable for the consequences.
Being negligent is the failure to exercise the standard of care that a reasonably prudent person would have exercised in a similar situation in order to protect others against unreasonable risk of harm. Determination of the appropriate standard of care is an issue of law. In general, a “reasonable person” standard of care is applied. Whether a defendant has met that standard of care is an issue of fact to be determined by the jury. Because “standards” that are adopted by associations or other nongovernmental entities may represent a consensus regarding what a reasonable person in a particular industry would do, such standards may be helpful to the trier of fact in deciding whether the defendant has met the standard of care that is due in a particular situation. Hansen
v. Abrasive Engineering and Manufacturing, Inc, 856 P.2d 625, 628 (Sup. Ct. Or. 1993).
Price on testo 330 combustion boiler testing,hand card testo p call 718 341-1314 or email.me
ReplyDeleteThe author makes a lot of good points; however, the main point is missed. That point is; the number one way to test for the combustion and overall health of the furnace/boiler/water heater is to check the CO level of the flue products. High CO levels can originate from mechanical problems other than in the combustion chamber. If the CO level is above normal there is a problem with the equipment that needs to be addressed.
ReplyDeleteBy checking just three things, the vent & combustion air system, the temperature rise and the CO, the technician has accounted for 95% of the potential problems with the heating equipment.
If the equipments health is good, the people living/working there will be healthy also.
First, thank-you for taking the time to post a comment.
ReplyDeleteWhile I do wholeheartedly agree that an appliance making CO needs repaired, the CO is rather a symptom of poor combustion than an indicator of appliance health. In other words, it may not be fault of the appliance at all, but rather that it was installed without provision for combustion air. Stability of the combustion process and its ability to operate safety within the building envelope are no less important. Consider this, how long will an appliance operate safely, possible producing no CO at the time of testing if the combustion air is slowly reduced due to a competing appliance like a cloths dryer or exhaust fan. As a contractor, we need to make sure that the appliance will operate safely under all conditions and specifically worst case depressurization conditions that could provide a pathway for combustion gasses to enter the home or the appliance operation to be compromised. That was the point that I was trying to convey.